As seen on Plumbing and Mechanical - June 23, 2014
Energy efficiency and mobile monitoring are driving the market
Technology is a rapidly changing universe and pump technology is no exception. With newer pumps comes increased reliability in the products, and convenience, security and comfort for the user. And with every type of pump there is something different to look for.
"Pumps available now as well as those coming into the market will increase efficiency, save costs and provide peace of mind for their customers — especially in mobile and remote offerings," says Mark Huntebrinker, director of marketing for Zoeller Pump Co. Users want and need to be assured they will be protected from things such as water in the basement, loss of valuables and the difficulties of dealing with insurance claims.
The push for higher efficiency has been a powerful call to action over the past decade. "Variable-speed pumps are designed to match circulation of hydronic fluids to precisely meet the call for heat; it's all about efficiency — something we're very proactive about," says Gene Fina, senior product manager for Taco. With the new Department of Energy rulings on efficiencies for commercial and industrial pumps, Taco is tailoring some of its work to develop technology that will further enhance system energy efficiency.
Van Johnson, senior portfolio manager for surface pumps at Franklin Electric, agrees that efficiency is the name of the game. Because many of the old constant-speed systems don't operate at full capacity, turning them on and off wastes energy and money.
"The new systems use variable-frequency drives, which vary motor speed to support variable flow and maintain constant pressure," he says. "This can greatly reduce power usage."
Brent Ross, global director of configured building equipment for Armstrong Fluid Technology, believes that what contractors really need to understand has less to do with new technology and more to do with cost control and project profitability.
"Contractors need to understand that the 'new' technology is now a decade old and they should not be afraid to install mechanical products with integrated digital controllers," he says.
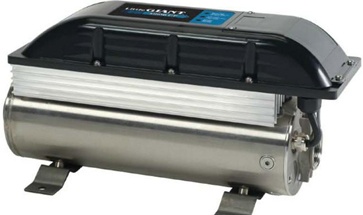
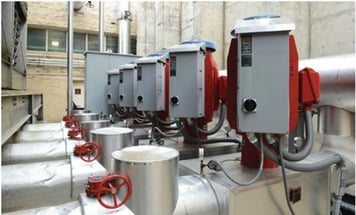
Ross still sees contractors passing up opportunities to reduce the installed cost because they focus on the lowest possible purchase cost, ignoring potential added costs for related components and installation labor. "By taking such a narrow view of their purchasing activity, they pass up opportunities for increased profitability, increased customer satisfaction, faster project completion and reduced risk," he explains.
Having visited with 50 contractors during the last few months, Hans L. Kuster, president of AquaMotion, says there are few contractors today who are not aware of the annual operating cost of the different circulators they install. "Estimates ranged from $40 to $250 per pump per year," he says. "Actual energy cost of our most efficient permanent split capacitor circulators is $16 to $19. They must educate themselves of the true annual energy cost of the pump they install and help the homeowner save on energy costs?'
Driving forces
Recently there has been a push for higher energy efficiencies as well as mobile and remote monitoring. Building and property owners, management companies, manufacturer entities and even electric utilities are taking a much greater interest and a closer look at efficiency gains, says Terry Teach, business development director, domestic buildings, at Grundfos Pumps Corp.
"The rising cost of energy and resulting need to decrease power consumption are the driving forces behind all technological advances in the pumping industry, whether residential, commercial or industrial," Johnson says.
Huntebrinker states an increase in material waste such as baby wipes and other items that should not go down a toilet is another driving shift for sewer pumps. "Traditional solid-passing sewage pumps are still a great option, but grinder pumps are gaining momentum in the market — especially in tough commercial applications;' he says.
One entity in particular is drawing a strong interest to new technology and high-efficiency products — electric utilities.
With investment in new technology comes a broad expectation that it will lead to improved energy efficiency, Fina says.
"Aside from replacement work, this is the most frequent impetus for change," he explains. "However, even with replacements, an investment in new equipment is weighed against an expected return — most frequently tied to fuel usage, but also to improvements in installation time, performance and comfort, perhaps even by means of remote monitoring and control."
The greater interest in mobile and remote monitoring is fueled by the power of information and advanced control technologies. The evolution and cost-effectiveness is becoming a benefit to all that use it.
"At the homeowner level, you're really starting to see some trends that support the desire by homeowners to have advanced control technologies within their homes for convenience, security and comfort," Teach says. "You also see a greater appetite by homeowners for information — understanding how their mechanical systems operate, what it costs to run a furnace or hydronic heating system and what the cost of water is in the home:'
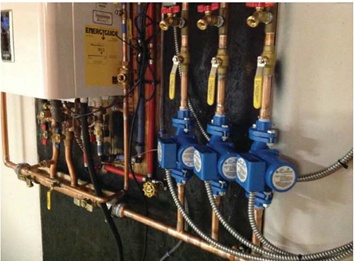
Security, comfort and more
Newer pump technology can benefit both homeowners and business owners. Key advantages on the commercial side are reduced power consumption and longer system life. A system works more smoothly when all its parts are in top shape. As pumps are tuned to the system for the best possible efficiency, all components within a pump system should be designed to work in concert with one another.
"Self-sensing pumps are built with pump performance curves embedded in the memory of the speed controller," Fina says. All components within this pump's system perform optimally, with much less effort, stress and energy consumed." Reducing the speed of a pump by half can save 200 million to 500 million shaft rotations per year, significantly reduce wear-and-tear and increase the seal's lifespan.
Energy-saving measures are a factor in owning a home or running a business. Johnson comments that prior to the use of VFDs, the pressure in any pump system would fluctuate, causing shortages when the system required high volume, such as when the washing machine, dishwasher and multiple showers are in use at the same time. The only available way to meet maximum needs was to upsize the system.
"Today's technology, through the use of constant-pressure systems, offers consistency and reliability in water delivery with lower energy costs," he says. "'Smart pumping' technology has given hydronic contractors more savvy equipment that can provide more consistent, comfortable temperatures at a lower cost."
Teach agrees: "Homeowners experience not only the best value at operating cost, but one that is easier to set up, understand and operate. Depending upon where a homeowner might be located, the interest in efficiency can vary but certainly with electrical costs there is an increased level of interest in saving as much as you can."
He points out one entity in particular that is drawing a strong interest to new technology and high-efficiency products — electric utilities. Because their business model is predicated on growth, they have a very high interest in seeing all building types and all users of pumps install high-efficiency pumps. Utilities don't want to build new power plants, as it is neither cost-effective nor environmentally desirable. Their interest and their best form of capital investment is to invest in high-efficiency products.
"They will often rebate high-efficiency products to the point where it makes it very effective for contractors to install them to the benefit of the end users;' Teach says.
Learning network
With all the different available pumps, training can be a very useful and sometimes necessary tool for contractors. There are many different ways a company can train its employees, including classroom and hands-on training, webinars, industry events, online courses and how-to videos.
Huntebrinker notes that Zoeller provides factory training for its reps, wholesalers and contractors several times a year at its training facility in Louisville, Ky., which includes classroom lectures, hands-on training with products and a comprehensive plant tour.
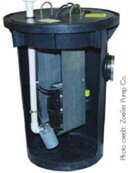
Taco provides training at its factory as well as in the field and online. "We routinely go into the market to hold remote training sessions in conjunction with manufacturers reps, often at their location, or hosted by a wholesaler," Fina says. The company also conducts training at its new Innovation and Development Center, which includes classroom spaces, conference rooms, a business center and functional labs for testing and teaching.
Franklin Electric offers monthly training to contractors through Franklin Tech at its Wilburton, Okla., and Grant County, Ind., facilities, says Kyle Lanier, portfolio manager at Franklin. Training also is provided at customer sites through its Mobile Training Facilities equipped with its products. In many states, the company offers eight-hour seminars in which students learn how the systems work and specifics on troubleshooting.
Grundfos has two- to three-day training activities as well as traditional lunch-and-learns at its facilities or wholesale locations. Webinars cover topic-specific items and new product introductions. In addition, the Grundfos Ecadamy was just announced at the AHR Expo in New York City this year.
"We are trying to put together a venue of training opportunities that suits the needs of the contractor community," Teach says. "Not everyone can travel so we want to provide core elements of the training to a contractor who desires to further himself, his awareness and his education of the latest technology."