As seen on pmengineer.com - May 27, 2015
When making such a significant investment into a company’s operations, it is smart business sense to have some protection built in.
That certainly is the true with Texas Instruments’ latest facility in Sugar Land, Texas.
TI, a worldwide semiconductor design and manufacturing company, along with an engineering team led by Project Manager Kenny Roland, P.E., with Houston-based DBR Engineering Consultants, went the whole nine yards in safeguarding the Sugar Land operation, which opened with a ribbon-cutting ceremony July 23, 2014.
The team installed Armstrong Fluid Technology pumps in the 160,000-sq.-ft. structure. Armstrong 4600 horizontal split-case base-mounted pumps were installed, featuring high-efficiency NEMA-premium motors for low energy consumption. According to Roland, this was not the original plan. He notes Texas Instruments at first desired to have a diesel pump installed.
“This system was actually designed multiple times,” he recalls. “It was revised to an electric pump, and relocated within the building because of the prohibitive nature and space necessitates associated with room requirements.”
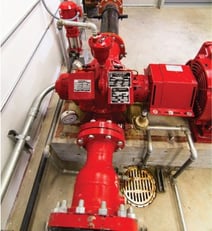
Additionally, the building has Armstrong 4700 vertical multistage pumps that feature fire safety “jockey” systems and casing venting to prevent air entrapment and dry running. Once all parties agreed on the Armstrong pumps, designing the facility’s fire protection system started with a simple test.
“The first step in our design was to obtain a flow test to determine the pressures and flows available near our surrounding site,” Roland states. “From this point, we provided detailed calculations to determine the overall pressure losses the system would occur when in operation.”
The Armstrong pumps met the requirements of the National Fire Protection Association’s codes, specifically NFPA 13, 14 and 20. Roland worked with his local Armstrong Fluid Technology representative — Jeremy Brown with Houston-based Texas Fire Pump Sales — on maximizing Texas Instruments’ fire protection solution.
“Once the pressure loss and demand was figured out, we teamed with (Brown) in an effort to provide the most efficient and economical pumping system,” Roland says.
Texas Instruments pushed Roland and his team to go above the minimum fire protection code requirements. In response, Roland fitted the building with a system that serves an ordinary hazard application, while the garage unit has a dry manual standpipe system.
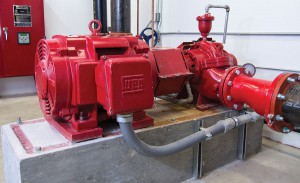
“The client requested all the fire protection system and piping be both UL and FM listed. They wanted to ensure quality and durability for this system,” he states. “They also requested the facility be protected by a higher-than-code-required hazard.”
Cost savings on the back end was another reason why Roland felt comfortable specifying the Armstrong pumps for Texas Instruments. The services Brown and his team at Texas Fire Pump Sales would provide the facility were critical as well.
“Allowing for optimal churn rates and operation at a lower horse power enabled the owner to save money and reallocate resources to other areas within the facility,” Roland says. “We also proceeded with Armstrong because in our area their personnel are unparalleled when it comes to customer service.”
Following the flow
Roland designed the building’s plumbing system to be in compliance with the 2009 International Plumbing Code with amendments made by the city of Sugar Land. The facility is supplied by city water, which goes through a triplex water softener system located in the garage building where the piping is routed underground and into the main building.
“Then the water is pumped by electric duplex domestic water booster pumps,” Roland says. “Each pump is provided with an integral variable frequency drive.”
Peak demand at the facility is 110 gpm at a total developed head of 115 ft., Roland states. For the storm and sanitation pipes, Roland called for cast iron with no-hub fittings and couplings. The fire protection system uses black steel pipe.
The building has about 920 ft. of domestic water and Roland went with Type L hard-drawn copper tubing for the core and shell portion.
“We used a point-of-use approach,” he says. “All the core building restrooms have an instantaneous electric tankless water heater, allowing for water and piping savings. Also, since no hot water has to be stored and maintained at a certain temperature and there is no recirculation pump it provides excellent energy savings.”
The Texas Instruments building utilizes Kohler fixtures and TOTO Smart Senor System faucets in the men’s and women’s restrooms. The TOTO faucets use the company’s EcoPower technology featuring a water-powered turbine that creates an electrical current creating renewable energy for each unit.
“This technology enables the faucet to extend the battery life,” Roland says.
The Texas Instruments campus has an Innovation Center showcasing demos of the latest company technology; numerous collaboration spaces; an employee courtyard; outdoor basketball and volleyball courts; and a fitness center and walking path around the building.
Roland says: “For a higher demand area such as the shower and locker room we supplied a tank-type water heater since this was a better fit for this type of application.”
The air side
Another element Roland highlighted was a compressed air system that has a main 3-in. air supply line that runs nearly 500 ft. The compressed air system segues in multiple branches to the lab facilities at the Texas Instruments offices.
“The compressed air system is critical for the laboratory and testing facilities,” Roland notes.
The system consists of two air compressors with two-stage speed drives that are water-cooled and oil-free, two zero-purge desiccant twin-tank air dryers and an ASME-rated vertical air receiver (128 in. by 36 in.) storage vessel with a storage capacity of 500 gal.
“Efficient, high-quality and oil-free compressed air was desired,” Roland says. “This system is tied into the building automation system to monitor — on or offsite — and is fitted with two separate compressed air meters to monitor air production and consumption.”
Roland felt it was critical to incorporate the compressed air in as flexible a manner as possible. One reason why copper pipe was used is because Texas Instruments can adjust the piping when needed.
“Copper piping is great for compressed air,” Roland states. “In the future if there is any need for modifications or additions, this type of pipe enables the client to easily incorporate, repair or cap portions as desired. It is a great system that will serve Texas Instruments for many years to come.”
In the community
Texas Instruments has invested more than $8 million into the Sugar Land region throughout the past 10 years. Roland adds when the company selected the location of its new campus, it went with an area close to public transportation routes.
The physical structure site reduces the average distance for its employees to the building, saving driving time. Additionally, the company provides preferred parking for fuel-efficient vehicles. Roland reports the campus is in the midst of pursuing a LEED Silver certification from the United States Green Building Council.
“The building is currently in the final construction submittal review,” he states.
Roland and his DBR associates worked on the Texas Instruments project for 17 months. Roland does not recall a specific challenge that had to be met, but says making sure all the details were ironed out before completion was critical.
“There were several small milestones for this project,” he says. “The coordination of all the different requirements and specifications from the client helped in creating a better pathway for a smooth project. We had a great team to work with and also great input from the client overseeing the team. After several meetings and coordination sets later, we arrived at the project we have now.”
Also seen on:
digital.bnpmedia.com - May, 2015