As Seen On: constructionweekonline.in July 6,2022
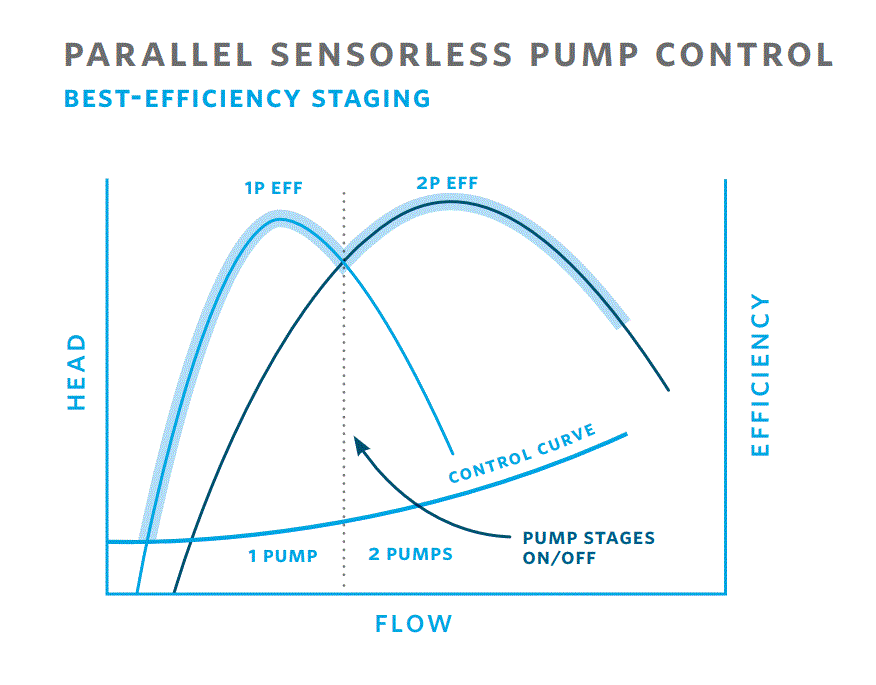
It’s important for HVAC system designers to understand that the relationship between pump costs and pump size is not a simple straight line. As pump sizes increase, the costs for the equipment, related components and installation increase faster. The result is that a pumping system that serves an HVAC load using two small pumps is less expensive than buying and installing one large pump.
A parallel configuration also allows appropriate handling of redundancy, where HVAC systems are required non-stop. In a two-pump system, if one pump fails, the remaining pump can serve the system requirements with up to 70% flow redundancy. Based on the building type and duty requirement, the capacity split can be adjusted. The chart presented lists different building types and the appropriate flow redundancy and capacity split, given the importance of the HVAC system to the building function.
Even with a 100% capacity split, parallel systems offer installed cost and operating cost savings. With lower levels of capacity split, the pump sizes are smaller and the installed cost savings are even greater.
What’s more, the savings go beyond installed costs. In response to temperature fluctuations, HVAC systems operate at a wide range of levels, from 100% to well below 50%. Because of the seasonality of temperatures, 100% output is required for a only a small percentage of total operating hours. For the vast majority of operating hours, HVAC systems are at part load. Because of these operating demands and the shape of pump efficiency curves, an HVAC pump system design using two or more smaller pumps is more efficient than one larger pump. Sharing the load across multiple pumps, and staging the pumps as required, allows the system to leverage the best efficiency range of individual pumps and all the pumps together.
HVAC loads and flow requirements change throughout the day. In the graphs presented, the grey dotted line intersecting the pump efficiency curves represents the flow level at which one pump in the array should be staged on or off. The solid grey line indicates where pump staging often occurs in system that relies on speed-based control. This approach to staging forces the pumps to operate at efficiency levels that are less than optimal. In a parallel pumping installation (up to four pumps) Parallel Sensorless Pump Control tracks and stages pumps at the correct levels to optimize efficiency.
Parallel Sensorless Pump Control technology stages pumps based on operating efficiency rather than motor speed. This approach improves the efficiency of the full pump array by up to 30% over traditional multi-pump installations. For any future pumping systems you design or purchase, consider the potential savings available through parallel redundancy and PSPC technology.