As Seen On: facilitiesmanagementadvisor.blr.com November 1, 2021
As the COVID pandemic gradually subsides, facility managers and HVAC professionals worldwide face the challenge of safely bringing buildings back online.
While ensuring the mechanical system is ready to handle the many challenges of increased occupancy is important, minimizing the possible transmission of SAR-CoV-2 is critical. The following article is designed to provide facility managers with helpful guidelines they can follow to bring their overall HVAC system—including the hydronic system, airside system, and plumbing system—back to full operating capacity.
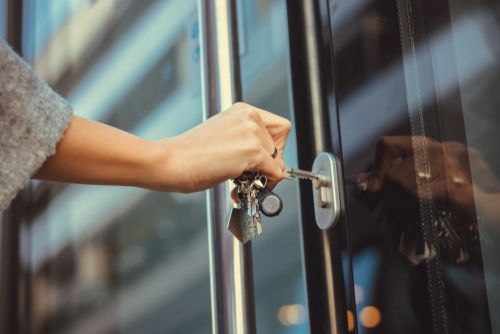
The first step in the process is to develop a comprehensive action plan that should include procedures not only for the systems listed above, but also for the domestic water distribution system. This includes system flushing plans and bacteriological testing if the system has been dormant for an extended period.
Air Handling Systems
Let’s begin with the air handling systems. The first rule is not to defer scheduled maintenance, as it can lead to decreased performance and reduce the likelihood of spreading airborne organisms.
Other helpful guidelines include:
- Develop a plan for safe changing of filters and cleaning of air handling equipment;
- Determine what PPE is required (masks, eyewear, gloves, etc.);
- Properly dispose of dirty filters—in sealed bags/boxes immediately removed from the building;
- Disinfect air handler interior surfaces;
- Ensure that coils and drain pans are clean and free of debris; and
- Verify that condensate drains properly.
The next item to address is ventilation with outside air. It is ideal to operate air building systems at 100% outside air for a minimum of one week and then institute a complete building air-side flush a minimum of 2 hours prior to occupancy daily.
This should be done early in the morning before air significantly warms, but be mindful of your particular climate. In areas of high humidity, cooling may need to be in operation to provide dehumidification. Use caution in colder months to ensure the buildings’ heating coils are capable of maintaining a reasonable leaving air temperature.
And, of course, verify that all outdoor intakes are clear and free of dirt, debris, and insects.
Heating Hot Water Systems
The next step is to focus on your heating hot water systems. It’s important need to test and check the boiler and all operating and safety controls. This includes verifying that:
- the burner cycles properly through the full firing range;
- all safety controls properly shut down the burner if unsafe conditions occur;
- the burner is operating at the correct firing rate and that the air-fuel ratio is correct—perform a combustion test to verify; and
- chemical testing of the system fluid has been done to verify chemical treatment levels are correct.
Chilled Water Systems
The next item on your action plan should the chilled water system. You need to carefully check the chiller and all operating and safety controls to verify:
- The compressor cycles properly to maintain leaving water setpoint;
- All safety controls properly shut down the chiller under low water conditions;
- Refrigerant charge is correct;
- The oil level is correct (for oil-lubricated machines);
- Proper cooling tower operation for water-cooled chillers; and
- Condensate fan operation and clean condenser coils for air-cooled chiller.
It is also important to perform chemical testing of the system fluid to ensure that chemical treatment levels are correct. If the system is filled with a heat transfer fluid, verify the concentration to ensure it’s correct.
Chilled Water System Efficiency
Since you are focusing on the chilled water plant, now would also be a good time to determine if your system is operating at optimum efficiency.
Chiller plants are not typically designed to operate for extended periods at reduced loads. Given the probability that your building has been operating at reduced capacity, you should reevaluate the best solution to reduce operating costs.
There are a variety of chiller optimization solutions and products on the market that can help you significantly reduce your operating costs. You should check with your consulting engineer or manufacturer representative to determine what is best for your facility.
Fluid Handling Systems
Next up on your action plan should be the fluid handling system. There are several items that need to verified:
- Ensure that make-up water systems and backflow prevention devices are operating properly;
- Check that expansion tanks are not water-logged and that bladder tanks have the correct air charge (per manufacturers’ recommended procedures);
- Confirm that all control valves operate smoothly throughout the entire operating range;
- Check and repair any leaks at valve packing;
- Inspect the system distribution pumps—lubricate as required, and check and repair any leaks; and
- Check all electrical connections—verify proper operation of variable speed drive or motor starter.
Cooling Towers
Cooling towers present special hazards due to the potential for biological growth, so it’s imperative that you check to ensure:
- All surfaces do not have the presence of algae or other biological growth;
- The chemical treatment system is operating properly and that chemicals are being properly dosed into the system;
- The water distribution systems are clean and operating properly;
- Hot water basins are clean and nozzles are clear;
- Spray nozzles are clean and evenly distributing water; and
- Water tower level is being maintained at the proper level and not overflowing.
Domestic Water Systems
Domestic water systems that have been idle for extended periods can develop bacteria blooms due to lack of chlorine and lack of fluid movement. Prior to occupancy, the entire domestic water system must be thoroughly flushed at each fixture.
This flushing must cover both the hot and cold water systems. Once the system is thoroughly flushed, bacteriological testing should be performed to verify that there is no bacteria present within the system.
Proper disinfection is the key to safely reopening buildings. The entire plumbing system should be completely disinfected by chlorination, to the minimum standards of AWWA C-651 and C-652. Flow should be established at all cold and hot outlets until a chlorine level of 5 PPM is obtained.
The system should then be allowed to stand for 24 hours and then rechecked for chlorine residual. If residual is less than 3 PPM, the system must be re-chlorinated.
The reason this is so critical is that 95% of bacteria in drinking water systems are in biofilms. Unfortunately, many different bacteria concentrations can occur in the various building plumbing systems.
Final Thoughts
By following these guidelines you should be ready to safely reopen your buildings. However, there are a few additional things to keep in mind:
- Be diligent in your efforts. Don’t cut corners to save time;
- Be aware that every change you make will affect another part of your building’s system;
- Be prepared for rapid changes—new variants and pathogens are likely to present new challenges;
- Seek out knowledgeable professionals who can not only help you safely reopen idle buildings, but also improve the overall efficiency of your operating system; and
- ASHRAE is a great resource for additional information on this topic.
- Armstrong has created a webinar on safely reopening buildings that you can access here.
Armstrong Fluid Technology is also a sponsor of an upcoming Facilities Management Advisor webinar, titled “Facility Risk Management in a Pandemic.” The online educational event will be held Tuesday, November 9, and registration is available for FREE here.
Tony Furst, MSed, CPD, LEED AP, is RSEC Manager at Armstrong Fluid Technology. He is a mechanical engineer with over 30 years of success overseeing all phases of multimillion-dollar construction, infrastructure, and energy projects for government and private-sector clients. Experience includes in-depth knowledge of district heating and cooling plants and distribution systems, automatic temperature controls, combustion systems and controls, and building code and standard industry practice.
Also Seen On
- ehsdailyadvisor.blr.com - November 2021